The Top 20 Fleet Management Challenges Faced By Owners and How to Overcome Them
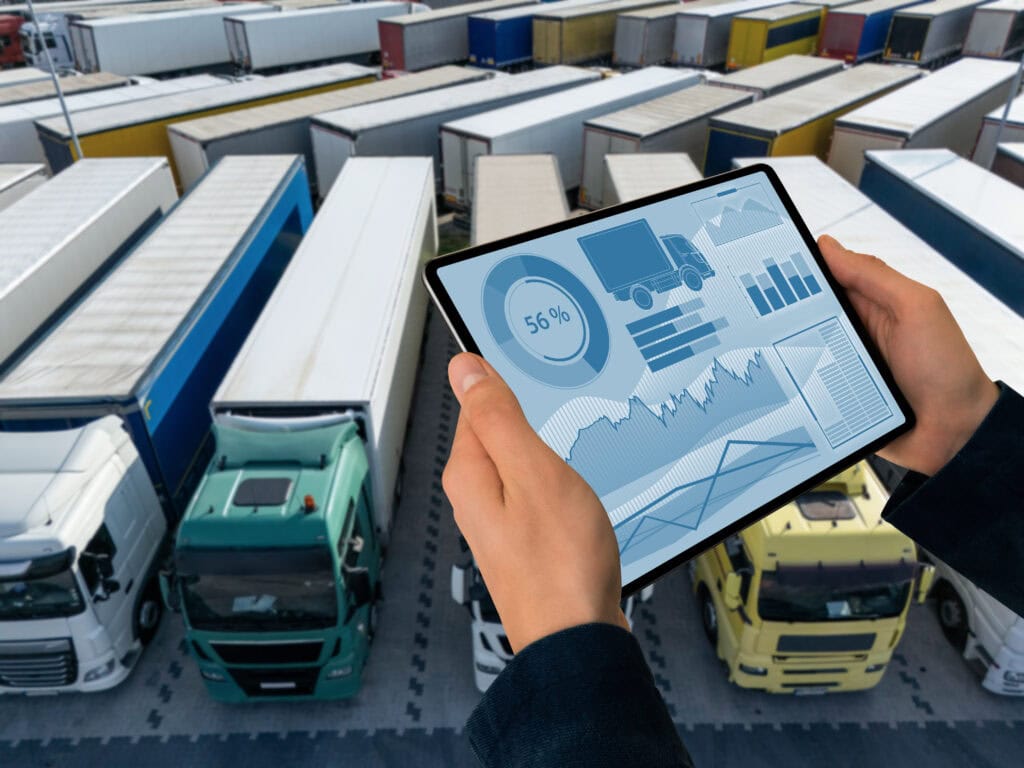
Solving fleet management challenges helps fleet managers reduce fuel costs, lower maintenance costs, and improve driver performance. Tools like GPS tracking, route optimization, and telematics systems enable smarter, informed decisions.
Rising fuel prices. Tight labor markets. Mounting pressure to deliver faster. Fleet owners face real problems daily, and these fleet management challenges aren’t going away anytime soon. Every delay, accident, or inefficiency costs money—and sometimes, even customers.
Whether managing five fleet vehicles or five hundred, staying ahead means knowing what’s working and what’s not. This guide breaks down the current state of the fleet industry and uncovers the top hurdles fleet managers deal with today.
The Current State of the Fleet Market
Faster delivery demands, supply chain issues, and rising fuel costs challenge fleet managers constantly. Balancing speed, cost, and reliability requires smart planning.
Tools like fleet management systems and GPS tracking boost fleet efficiency. Adapting to regulations, maintenance expenses, and economic shifts demands real-time data and scalable fleet management solutions.
The Importance of Identifying Fleet Management Challenges
Fleet success depends on clear visibility into everyday risks and inefficiencies.
- Risk Mitigation: Spotting fleet management challenges early reduces accidents, breakdowns, and major safety risks.
- Strategic Planning: Identifying challenges improves decisions, strengthens systems, and keeps fleet managers competitive.
- Resource Optimization: Targeting issues boosts vehicle performance, lowers maintenance costs, and improves driver productivity fleet-wide.
Top 20 Fleet Management Challenges
Rising costs, tight regulations, and growing demands push fleet managers to rethink how they manage vehicles, data, and drivers every day. Here are the top potential challenges:
1. Managing Operational Costs
Uncontrolled operational costs drain profit. Use fleet management software to track expenses, flag waste, and gain visibility. Analyze fuel usage, driver hours, and vehicle maintenance patterns.
Cut hidden costs by reviewing service contracts. Streamline processes through automation and eliminate inefficient workflows. Smart controls lead to better budgeting and stronger fleet performance over time.
2. Supply Chain Disruptions
Supply chain disruptions delay parts, deliveries, and schedules. Build backup suppliers and diversify vendors. Use fleet management systems to monitor inventory levels and plan ahead.
Invest in real time data to stay updated on traffic, weather, and delivery windows. Agile fleets adapt faster and keep fleet operations stable even during volatile periods.
3. Vehicle Acquisition
Buying fleet vehicles without planning can lead to financial strain. Set a replacement schedule using fleet management solutions. Track vehicle performance and depreciation.
Lease newer models when budgets are tight. Monitor usage data to buy only what fits your needs. Better acquisition planning cuts long-term fleet expenses and improves your overall asset strategy.
4. Inefficient Fuel Management
Poor fuel management increases waste. Install GPS tracking and telematics to monitor fuel consumption in real time. Encourage efficient driving habits through driver training programs.
Identify route delays and engine idling using data analytics. Reducing unnecessary fuel usage directly lowers operational costs and boosts fuel efficiency across the entire fleet.
5. Fuel Price Volatility
Fluctuating fuel prices break budgets fast. Lock in bulk fuel rates or use fuel cards with cashback. Monitor routes to cut unnecessary mileage. Promote efficient driving habits to lower fuel usage.
Use fleet management software to track fuel costs daily. Fuel control ensures fewer surprises and better forecasting throughout every quarter.
6. Improper Trip Planning
Inefficient routes lead to wasted time and higher fuel costs. Use route optimization tools to find efficient routes for every trip. Review traffic patterns and delivery schedules before dispatching.
Assign jobs based on proximity and vehicle load. Precise planning helps fleet managers improve delivery speed, reduce delays, and save on fuel and maintenance expenses.
7. Video Evidence
Lack of footage complicates accidents and insurance claims. Install dashcams linked to fleet management systems. Video provides proof, promotes accountability, and improves driver behavior. Review incidents for training.
Protect company assets by resolving disputes quickly. Combined with telematics, video reduces insurance premiums and enhances transparency across your fleet operations.
8. Driver Shortages
Finding skilled drivers is harder than ever. Offer competitive pay, benefits, and clear paths for advancement. Improve driver satisfaction through support and communication.
Invest in driver training programs to upskill recruits. Automate scheduling to reduce workload. A people-first approach helps fleet managers attract, retain, and grow talent for long-term operational stability.
9. Accurate Reporting
Inaccurate data leads to bad decisions. Replace manual logs with automated fleet management software. Sync maintenance records, fuel logs, and route data in one system.
Use dashboards for quick overviews and drill-downs. Trustworthy reporting improves data-driven decision making and helps spot issues early before they impact fleet performance or budgets.
10. Autonomous Vehicles
Adopting autonomous tech requires careful planning. Start small with assisted features like lane warnings or adaptive cruise control. Monitor vehicle performance closely and train drivers.
Understand legal requirements in your region. Blend automation with human oversight to ensure both productivity and vehicle safety improve without adding risk.
11. Electric Vehicle Popularity
The growing demand for electric vehicles creates new challenges. Install charging infrastructure and track usage. Use fleet management solutions to monitor battery health and range.
Plan trips around charge stations. Train drivers on EV handling. Compare running costs vs. fuel models. Smart EV integration improves sustainability and lowers long-term maintenance expenses and fuel consumption.
12. Integration of Emerging Technologies
New tech like machine learning, AI, and telematics requires smart adoption. Avoid being overwhelmed by starting small and testing one system at a time. Sync tech with existing fleet management systems.
Ensure all tools share data seamlessly. Use tech to improve driver behavior, optimize routes, and automate tasks for better operational efficiency and faster results.
13. Poor Communication
Miscommunication causes delays, missed deliveries, and errors. Equip teams with instant messaging tools tied to your management system. Train dispatchers to give clear, concise updates.
Use alerts for route changes or emergencies. Encourage driver feedback. Reliable communication helps improve driver productivity, minimize confusion, and keep fleet operations running smoothly at all times.
14. Health and Safety Issues
Unsafe driving puts people and assets at risk. Launch safety programs that monitor driver performance using dashcams and sensors. Set up alerts for harsh braking and speeding.
Use maintenance alerts to avoid breakdowns. Train staff on safety protocols regularly. Safer fleets reduce accidents, protect your company assets, and keep insurance costs down.
15. Ensuring Compliance Requirements
Missing regulations can lead to fines or legal issues. Stay current with laws affecting the fleet industry. Automate reports to track hours, inspections, and maintenance schedules.
Keep digital records for audits. Use compliance features in your fleet management software. Proactive compliance ensures your entire fleet stays legal, safe, and fully operational.
16. Adopting Green Practices
Sustainability matters to customers and regulators. Switch to fuel-efficient or electric vehicles. Use data analytics to measure emissions and track impact.
Cut idle time, reduce mileage, and improve routing. Adopt preventive maintenance to reduce waste. Greener practices improve brand image, lower emissions, and help reduce fuel consumption across fleet operations.
17. Maintenance Issues
Missed services lead to costly repairs and lost revenue. Use fleet management systems to schedule regular vehicle maintenance. Set up maintenance alerts and track service history.
Monitor wear and tear using sensors. Fix problems early to avoid unexpected breakdowns. Consistent maintenance lowers maintenance costs and extends life cycles of fleet vehicles.
18. Unexpected Breakdowns and Accidents
Breakdowns stall deliveries and damage trust. Use real-time data and sensors to monitor health stats. Conduct pre-trip checks and enable drivers to report issues fast.
Activate preventive maintenance to reduce failure risks. Create response plans for emergencies. Proactive strategies cut downtime, protect vehicle safety, and avoid disruptions in critical routes.
19. Driver Behavior & Performance
Poor driver behavior affects safety and costs. Track patterns like speeding, idling, and harsh braking through telematics. Use scorecards and gamification to encourage better habits.
Offer coaching and incentives. Good driving lowers fuel usage, extends vehicle performance, and reduces accidents, giving fleet managers stronger control over productivity and driver accountability.
20. Lack of Strategic Vision
Without a clear roadmap, fleet management stalls. Set short- and long-term goals tied to KPIs. Use data-driven decision-making to plan growth, manage company assets, and cut waste.
Review market shifts and adapt fast. Build flexible systems that support change. Strategic planning keeps fleet managers focused, agile, and future-ready.
Conclusion
Solving fleet management challenges helps fleet managers reduce fuel costs, lower maintenance costs, and improve driver performance. Tools like GPS tracking, route optimization, and telematics systems enable smarter, informed decisions. Ongoing strategy reviews help teams boost productivity and cut fleet expenses.