Articles
News
Global Business Leaders Feel Effects of a Riskier World
Nearly three quarters (72 percent) of business leaders in companies in Canada and around the world say their companies are increasingly impacted by risk and they believe we are living in a riskier world. That’s according to the BDO Global Risk Landscape Report, which surveyed 500 C-suite leaders, board and audit committee members from all […]
Read More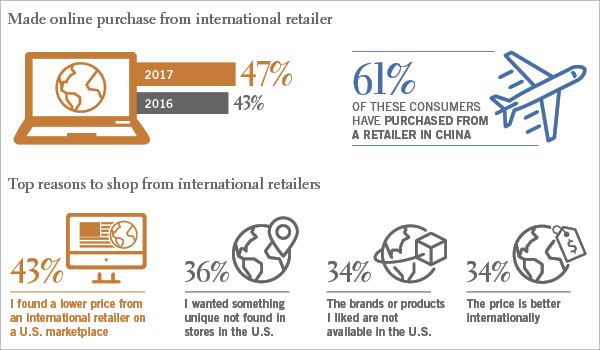
U.S. Online Shoppers Click With International Retailers
Nearly half of avid U.S. online shoppers bought items from international retailers, demonstrating the need for retailers to offer more personalized services as a way to compete against lower prices, according to UPS’ sixth annual Pulse of the Online Shopper study. Almost all avid U.S. online shoppers (97 percent), made purchases on marketplaces, up 12 […]
Read More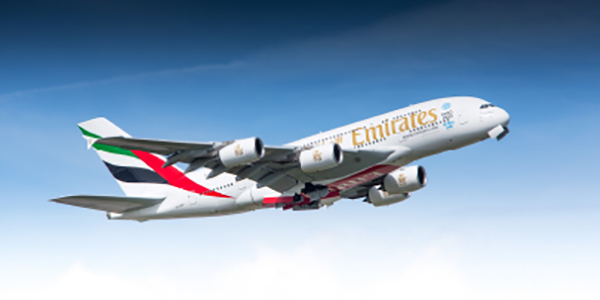
Global Supply Chain Suffers Disruptions Amid Diplomatic Crisis
Disagreements in the Middle East left the supply chain reeling as Saudi Arabia, Egypt, United Arab Emirates (UAE), Bahrain, Libya, and Yemen cut political and business ties with Qatar and accused the small Middle Eastern nation of supporting radical Islamic terrorism in the region. As part of efforts to sever contact, the countries shut down […]
Read More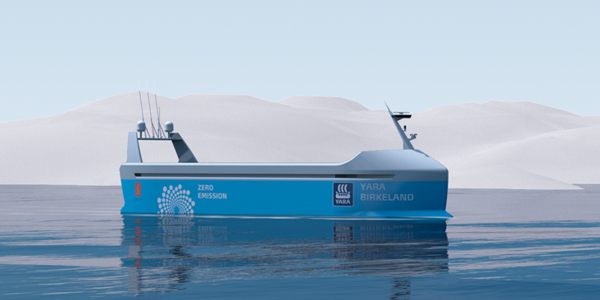
Could Self-Driving Ships Become Reality by 2020?
"This is happening. It’s not if, it’s when. The technologies needed to make remote and autonomous ships a reality exist." So said Oskar Levander, vice president of innovation for Rolls Royce, at Amsterdam’s Autonomous Ship Technology Symposium in 2016. He wasn’t wrong about the technology, considering the United States and China already have unmanned naval […]
Read More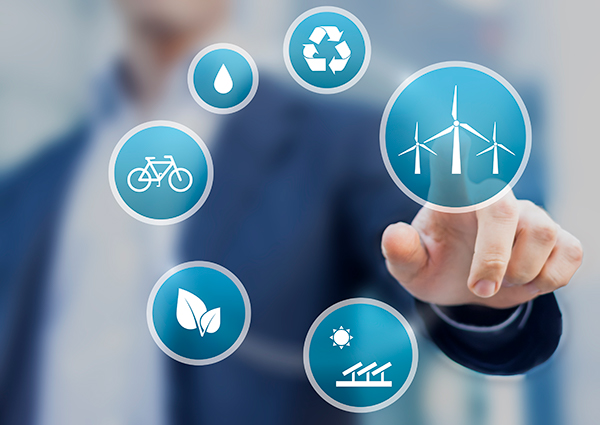
Supply Chains Double Down on Climate Change
President Donald Trump pledged to withdraw the United States from the Paris climate accord, but stakeholders involved with the American supply chain—often supportive of the President’s business-friendly policies—aren’t so ready to fall in line this time. Rather than push American businesses away from sustainable initiatives, many companies seem to have reaffirmed their commitments. A few […]
Read MoreManufacturing, Logistics Grew Dramatically Over Last Generation
Contrary to public perception, U.S. manufacturing and logistics experienced dramatic growth over the past generation, says a study by the Ball State Center for Business and Economic Research (CBER) and Conexus Indiana. U.S. manufacturing production grew 11 percent since the 2000-2003 dot.com bust and ensuing economic turbulence of the 2001 and 2007-2009 recessions, reports Manufacturing […]
Read More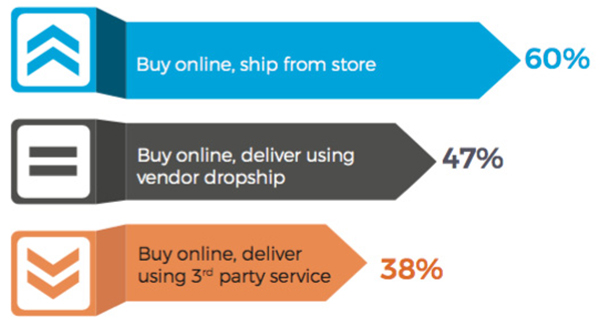
Retailers Struggle to Control Fulfillment Costs
Walmart’s recent announcement that it is testing a delivery system where its associates will deliver online orders to customers’ doors makes sense in light of a new study by Radial, in partnership with EKN Research, which finds the average cost for a company to fulfill an order is 70 percent of the average order value. […]
Read More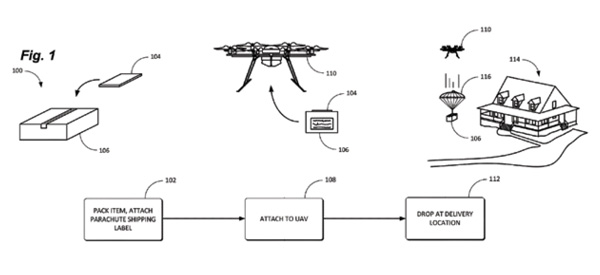
Amazon Files Patent To Parachute Packages
Amazon teased consumers with drone delivery during a 2017 Super Bowl commercial, though the ad bore a disclaimer: "Prime Air is not available in some states (or any really). Yet." Back in December 2016, Amazon made its first successful customer delivery in a trial area in the United Kingdom; in March 2017, the online retail […]
Read MoreSupply Chain Commentary: Grocery Retailers Need to Embrace Digitization Now
The grocery industry is entering a new stage in its evolution – a transformative stage that may cause some of the major players to lose competitive ground or, worse, impact their very existence. There is no secret here. Everyone can see what is about to happen to grocery retailers, because it already happened to other […]
Read MoreFreight Management and Route Optimization: A Critical Combination
There are significant opportunities for fleets to improve their operational efficiency with a combination of freight management and route optimization. The definition of freight management has transitioned over time, but whether your primary method of transport is via a freight broker, third-party integrated logistics provider, or your own private fleet, the problem is generally the […]
Read MoreMaking Sense of the $13B SCM Software Space
Gartner’s recent report that the supply chain management (SCM) software market will be worth more than $13 billion in the U.S. by the end of 2017 has likely turned many heads – both within the manufacturing and supply chain spaces, as well as with external audiences. In reality, this news that expenditures in this space […]
Read MoreChoosing a Freight Auditing and Payment Vendor
If you’re a freight shipper who is thinking about using a freight auditing and payment service, what should you look for in choosing the best vendor for your organization? These seven selection criteria present a straightforward process to penetrate beyond a company’s sales brochure and determine how well a service company can actually do the […]
Read More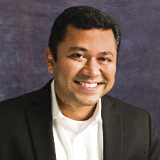
How Walmart’s OTIF Policy Creates New Baselines for Suppliers
Wal-Mart Stores Inc. caught many shipping companies off guard when it released its new “On-Time In-Full” (OTIF) policy. This program mandates that if any shipment arrives early, late, or on-time but not packaged properly, the shipper will be charged 3 percent of the total items’ value. It was only a few months ago that Walmart […]
Read More5 Ways Automated Dimensioning Helps Optimize First Mile Logistics
E-commerce is not just changing the retail industry, but significantly impacting logistics as well. Reaching $394.86 billion last year, e-commerce has increased 15.6% compared with $341.70 billion in 2015. With such an increase in e-commerce sales, the need for an efficient delivery service has never been so high. Customers are greatly influencing the delivery of […]
Read MoreReport: Multimodal Transportation Has a Future in Europe
Multimodal logistics moves freight by combining two or more transport modes. In this area, Europe still lags the more advanced U.S. market but has made steady progress. In its latest industrial research for the EMEA region Colliers International highlights a number of examples of established and emerging European multimodal platforms and discusses the drivers and […]
Read More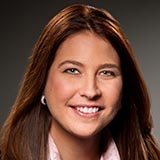
Supply Chain Commentary: Customer Loyalty Hinges on Quality of Product Information
Knowledge is power, and today, consumers are demanding to know more about products they buy before making a purchasing decision. The internet and online shopping have helped fuel their appetites for more product details, driving big changes across all industries. In the food industry, for example, new legislation like the GMO labeling law and Nutrition […]
Read More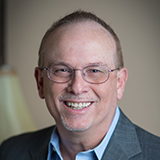
The Key to Lasting Supply Chain Innovation: Get Real
Managing a business for sustained growth often means finding and implementing innovative solutions to the challenges of complex supply chain logistics. Yet, when it comes to achieving lasting, repeatable innovation, it’s the real-world solutions that win out time and time again in leading logistics facilities. In his book Moneyball, Michael Lewis detailed how an analytical, […]
Read MoreDiscovering Eight Truths of the New Era of Retail
Over the past 20 years many retailers have had the dream of entering the food retail business. The appeal is undeniable huge revenues, repeat business and in-store traffic. The fascination has resulted in a proliferation of food retail models ranging from dollar stores, off-price stores, convenience stores, drug stores, supermarkets, discount supermarkets, premium supermarkets, farmers […]
Read MoreWhy Onshoring Manufacturing Requires Offshoring IT
Despite a slowing economy, U.S. manufacturers continue to add capacity stateside. According to a 2015 Boston Consulting Group survey, 31 percent of U.S. manufacturing executives said they were most likely to add capacity within the U.S., compared to only 20 percent opting to do so in China. This marks a stark reversal from 2013, when […]
Read MoreAre Warehouse Insurance Policies Covering Today’s Emerging Risks?
Warehouse legal liability insurance has always been one of the most misunderstood insurance contracts in existence. In general, insurance companies and brokers have limited industry knowledge and understanding of what warehouse operations entail. Not only that, but warehouse risks and vulnerabilities are increasingly complex, and many policies simply aren’t keeping up with today’s sophisticated new […]
Read More