Vendors vs Suppliers: The Differences and Why It Matters
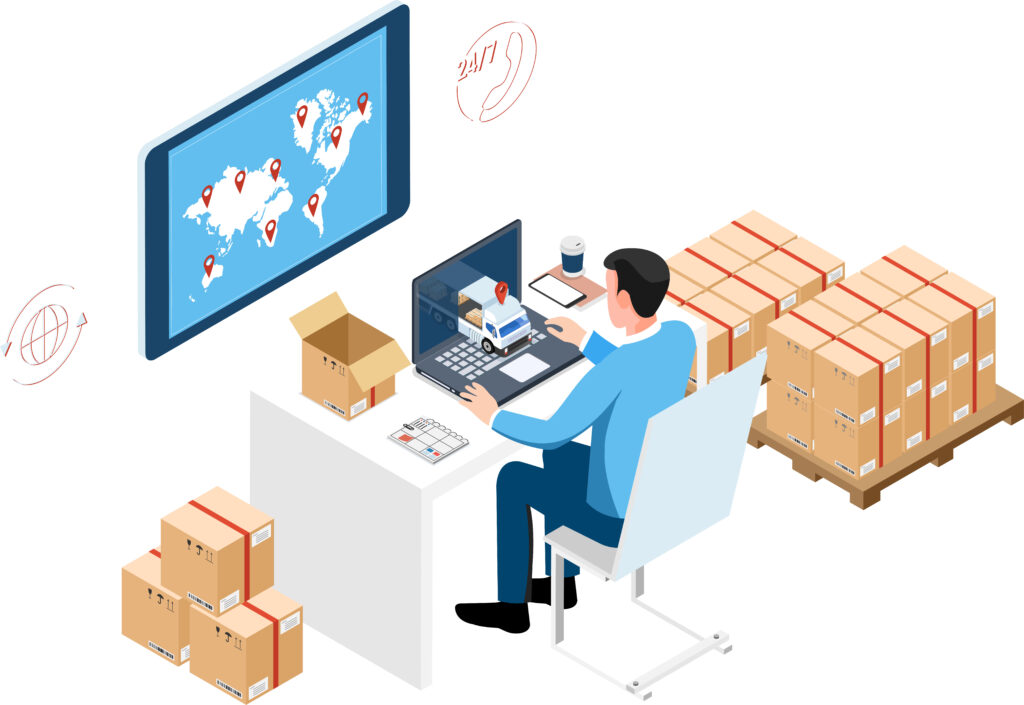
Vendors and suppliers are both business entities that play different roles in the supply chain. Suppliers provide raw materials, while vendors sell finished products to other businesses or the final customer, operating in distinct capacities depending on the products’ use and sales channels.
The key difference lies in what each business entity provides to the supply chain—suppliers offer raw materials, whereas vendors deliver finished goods.
Understanding this distinction helps improve inventory management, streamline the procurement process, and strengthen vendor and supplier relationships. Clear knowledge of these roles leads to smarter decisions in business operations and better supplier management.
This article breaks down the key differences, explores vendor and supplier roles, and explains how to manage each business relationship for improved operational efficiency and long-term success.
What is a Supplier?
A supplier is a business entity that delivers raw materials, components, or bulk quantities of goods to manufacturers, vendors, or retailers. Suppliers form the first link in the supply chain and play a major role in keeping the production process running without delays. Suppliers sell products in bulk to manufacturing companies or other resellers, supporting the flow of goods through the supply chain.
Suppliers help businesses maintain a steady supply of essential inputs used to create finished goods. Suppliers deal in large volumes or raw materials, which can significantly impact the efficiency of production processes. In a typical supply chain, suppliers focus on sourcing high-quality materials and ensuring timely delivery.
Strong supplier relationships help companies control costs, reduce downtime, and maintain product standards. Suppliers interact with businesses on a regular basis, supporting ongoing business processes. Efficient supplier management leads to smoother business operations and better supply chain management overall.
Utility companies are also key suppliers, providing essential services that a manufacturing company relies on to maintain smooth production processes.
Types of Suppliers
Suppliers fall into different categories depending on their role in the supply chain process:
- Manufacturers: Produce and supply goods from scratch. They often work with large quantities and offer direct delivery to other businesses for further processing or resale. Manufacturers are often considered manufacturing partners in the supply chain, playing a crucial role in production quality and operational workflows.
- Wholesalers: Buy in bulk quantities from manufacturers and resell them to retailers or smaller vendors. They serve as a cost-effective solution for small businesses needing access to finished products without producing them.
- Distributors: Act as a supply chain link between producers and vendors. They manage delivery schedules, warehousing, and ensure products reach the next stage on time.
- Importers: Importers bring in goods from international markets. They manage customs, logistics, and regulations, giving businesses access to finished goods or raw materials not available or affordable locally.
- Agents/Brokers: Agents or brokers connect vendors and suppliers without holding stock. They simplify sourcing by negotiating deals, improving supplier relationships, and saving time during the procurement process.
It’s important to note that not all suppliers are vendors; some suppliers only provide raw materials or components and do not sell finished goods.
Businesses rely on suppliers to provide raw materials consistently and support uninterrupted production and delivery cycles.
What is a Vendor?
A vendor is a business entity that sells goods or services to other businesses or individual consumers. Vendors operate in business-to-business and business-to-consumer markets. Vendors typically provide the finished product and tend to operate closer to end customers, often selling in small quantities. Unlike suppliers, vendors focus on selling the finished product directly to end customers.
Strong vendor relationships help businesses meet consumer demands, improve service delivery, and stay competitive in a fast-moving supply chain.
Types of Vendors
Vendors operate in different forms, depending on what they offer and who they serve. Each type plays a unique role in vendor management, customer service, and overall business practices. Understanding vendor types helps streamline the procurement process.
For example, a food truck acts as a vendor by purchasing ingredients from suppliers and selling prepared meals directly to end customers, serving as the last supply chain link and providing valuable feedback from consumers.
Retail Vendors
Retail vendors directly sell finished goods to the individual consumer. They often operate in fast-paced environments with high turnover rates. Meeting consumer demands quickly allows them to maintain strong product quality standards and build trust with shoppers across diverse retail channels.
Service Vendors
Service vendors offer services directly rather than physical goods. Examples include software vendors, IT support providers, or logistics consultants. These vendors deliver comprehensive solutions that enhance business workflows, support technological infrastructure, and improve operational efficiency for companies that depend on outsourced expertise.
Wholesale Vendors
Wholesale vendors distribute large quantities of finished products to retailers or other businesses. Offering competitive pricing and fast fulfillment, they support business scalability and growth. These vendors serve as a vital link between suppliers and the market across a broad range of industries.
Online Vendors
Online vendors directly sell products through digital platforms instead of physical stores. They handle orders via websites or marketplaces, offering finished goods to a broad range of consumers with flexible delivery schedules and convenient access across various regions or countries.
Drop-Ship Vendors
Drop-ship vendors sell products without storing inventory themselves. Orders go directly to other vendors or suppliers who handle fulfillment. This model supports small businesses, lowers overhead, and increases reach without managing physical stock or owning a warehouse infrastructure.
Vendors focus on selling finished goods, not on supplying raw materials, which sets them apart in the vendors vs suppliers comparison.
Key Differences Between Vendors and Suppliers
Vendor definitions and the terms vendor and supplier are often used interchangeably, but they have distinct roles in the supply chain. Vendors typically sell finished goods or services directly to consumers or businesses, while suppliers provide raw materials or components needed for production.
Understanding the key differences between vendors vs suppliers helps improve vendor management, enhance the procurement process, and strengthen every business relationship in the supply chain. The key difference between vendors and suppliers lies in the type of products they provide and their position in the supply chain: suppliers lie at the beginning, providing raw materials or parts, while vendors are at the end, selling finished products. Here are the key differences:
Supply Chain Positioning
Suppliers start the supply chain by delivering raw materials, while vendors end it by selling finished goods to retailers or directly to the individual consumer. Suppliers provide the input for production, and vendors push the final product to market for immediate use or resale.
Business Relationships
Supplier relationships often focus on reliability and long-term contracts that secure continuous access to large quantities of materials. Building a good relationship with both vendors and suppliers is crucial, as it fosters trust, open communication, and mutual success.
Vendor relationships, however, depend on adaptability, competitive edge, and the ability to meet shifting consumer demands across third-party relationships or external entities like distributors and resellers. Maintaining a positive working relationship helps resolve issues quickly and improves collaboration between all parties.
Procurement and Inventory Management
Efficient supplier management controls input costs and supports accurate production schedules. Vendor coordination aligns delivery with real-time sales needs. Businesses typically treat vendors as retail-facing, while suppliers are integral to production planning and inventory stocking across the entire value chain and supply chain management strategy.
Supplier Relationships and Management
Supplier relationships are the backbone of an efficient supply chain process, especially in business-to-business environments. Suppliers provide the essential raw materials that keep the manufacturing process running smoothly, making them a critical link in business operations. Effective supplier management ensures a steady supply of high-quality materials, which is vital for meeting consumer demands and maintaining production schedules.
Building strong supplier relationships goes beyond simple transactions. It involves developing trustworthy partnerships that support long-term business goals and supply chain optimization. By working closely with suppliers, companies can secure reliable access to essential raw materials, reduce the risk of disruptions, and improve overall supply chain efficiency. Strategic supplier management also allows businesses to negotiate better terms, maintain consistent quality standards, and respond proactively to changes in the market.
In summary, suppliers play a vital role in supporting other businesses by delivering the high quality materials needed for production, making supplier relationships a key factor in successful business operations and supply chain performance.
Vendor Management
Vendor management focuses on overseeing the relationships with vendors who deliver finished goods or services directly to consumers or other businesses. As the last link in the supply chain before products reach the final consumer, vendors are essential for ensuring that goods are available when and where they are needed. Effective vendor management is crucial for achieving timely delivery, maintaining competitive pricing, and ensuring the consistent quality of finished goods.
In the business-to-consumer market, vendor relationships are often more transactional and fast-paced than supplier relationships. Vendors must be agile, responding quickly to shifts in consumer demands and preferences. This requires a focus on direct sales, efficient order fulfillment, and the ability to provide quality products and services directly to the end customer. Good vendor management practices help businesses maintain a reliable flow of finished goods, meet customer expectations, and stay competitive in dynamic markets.
Ultimately, managing vendor relationships well is key to delivering value to the final consumer and supporting the overall success of the supply chain.
How Vendors and Suppliers Work Together?
Vendors and suppliers play connected roles in ensuring smooth business operations. Smart coordination between vendors vs suppliers helps meet customer expectations and avoid disruptions across the supply chain. Managing relationships between vendors and suppliers is crucial for building trust, maintaining transparency, and achieving effective collaboration.
While both are essential, businesses often form strategic ties with vendors and suppliers to secure reliable sources and maintain quality. A strong supplier relationship supports business objectives by fostering mutual goals, open communication, and long-term competitive advantage.
Leveraging technology, such as Specification Data Management software, can create a direct link between vendors and suppliers, enabling seamless access to partnership data for improved tracking, cost management, and supply chain optimization.
Supply Chain Integration
Vendors rely on suppliers to ship high-quality materials or goods on time to maintain a steady supply of finished products. Clear timelines and mutual understanding reduce delays, improve inventory flow, and strengthen positive working relationships across business-to-business and business-to-consumer channels.
Risk Mitigation and Strategic Partnerships
Strong supplier relationships and flexible vendor partnerships help minimize risks like shortages, delays, or cost spikes. Businesses form strategic ties with both a supplier and a vendor to maintain control, improve visibility, and secure access to innovative solutions that support operational efficiency and long-term business practices.
Business to Consumer Market Considerations
In the business-to-consumer (B2C) market, both vendors and suppliers must be highly responsive to changing consumer demands and preferences. Vendors, who interact directly with individual consumers, need to offer high-quality products and services that align with current trends and expectations. Their ability to quickly adapt to shifts in consumer behavior can make the difference between success and failure in a competitive marketplace.
Suppliers, while not always in direct contact with consumers, play a crucial supporting role by providing the raw materials necessary for production. They must ensure that their materials meet the quality and safety standards required by today’s discerning consumers. This means staying informed about market trends and regulatory requirements, and working closely with manufacturers to deliver materials that support the creation of quality products.
For both vendors and suppliers, understanding and anticipating consumer demands is essential for thriving in the B2C market. By focusing on quality, flexibility, and responsiveness, they can better serve individual consumers and contribute to a stronger, more resilient supply chain.
Suppliers Play a Crucial Role
Suppliers play a crucial role in the supply chain by providing the raw materials that are the foundation of the manufacturing process. Without a steady supply of high-quality materials, manufacturing companies would struggle to produce the finished goods that meet consumer demands. In a typical supply chain, suppliers are the first link, delivering essential raw materials such as components, ingredients, or other goods that are transformed during production.
The key difference between suppliers and vendors lies in the type of products they provide: suppliers deliver raw materials for further processing, while vendors offer finished goods ready for sale to the end customer. Understanding this distinction is essential for effective supply chain management and optimization, as it helps businesses ensure a reliable flow of both materials and products.
By recognizing the vital role suppliers play in maintaining a steady supply of high quality materials, companies can strengthen their supply chain, improve production efficiency, and better meet the needs of their customers.
Choosing Between a Vendor and a Supplier
Choosing between a vendor and a supplier depends on business goals, resources, and customer expectations. Both offer different advantages based on where a company fits in the supply chain and how it handles its procurement process.
- Nature of the business: Manufacturers rely on suppliers to get raw materials, while retailers need vendors who sell goods like finished products or office supplies.
- Procurement needs: Businesses needing bulk inputs use suppliers. Those looking to source final product lines prefer vendors for direct, ready-to-sell inventory. Choosing the right partner also helps ensure timely delivery of goods or materials.
- Customer demands: Fast-changing markets push companies to work with both a supplier and a vendor to meet demand for a diverse range of goods or services directly.
Choosing the right partner helps build good relationships and boosts long-term supply performance. The choice between a vendor and a supplier can significantly impact overall business processes and efficiency.
Conclusion
Understanding vendors vs suppliers helps businesses strengthen operations and make better sourcing decisions. Suppliers provide raw materials early in the process, while vendors sell goods at the final stage.
Vendors and suppliers serve unique purposes, but together complete the flow of finished goods through the supply chain. Strong vendor management and effective supplier relationships keep production steady, meet deadlines, and reduce supply disruptions.
Businesses that manage vendor vs supplier strategies well gain a competitive edge, improve the procurement process, and maintain good relationships that support growth and stability.