Articles
Knowledge Center
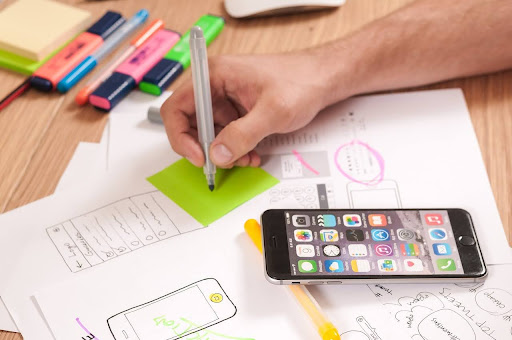
Procurement Process and SCM: Processes, Types, How They Differ, and How to Integrate Them
Every business relies on suppliers to keep things moving. Without the right products or services at the right time, operations slow down, and customer satisfaction drops. That’s where procurement in the supply chain steps in—it’s not just about buying stuff; it’s about making smart, strategic decisions that drive performance. Procurement in the supply chain refers […]
Read More
Urban Warehousing: What It Is, Characteristics, and Benefits
Last-mile delivery has become a serious challenge for many businesses. Online shopping is growing fast, but getting products from warehouses to customers in urban areas is harder than ever. Roads are packed, customer expectations are high, and delays lead to lost sales. As cities grow and e-commerce booms, the demand for effective urban warehousing solutions […]
Read More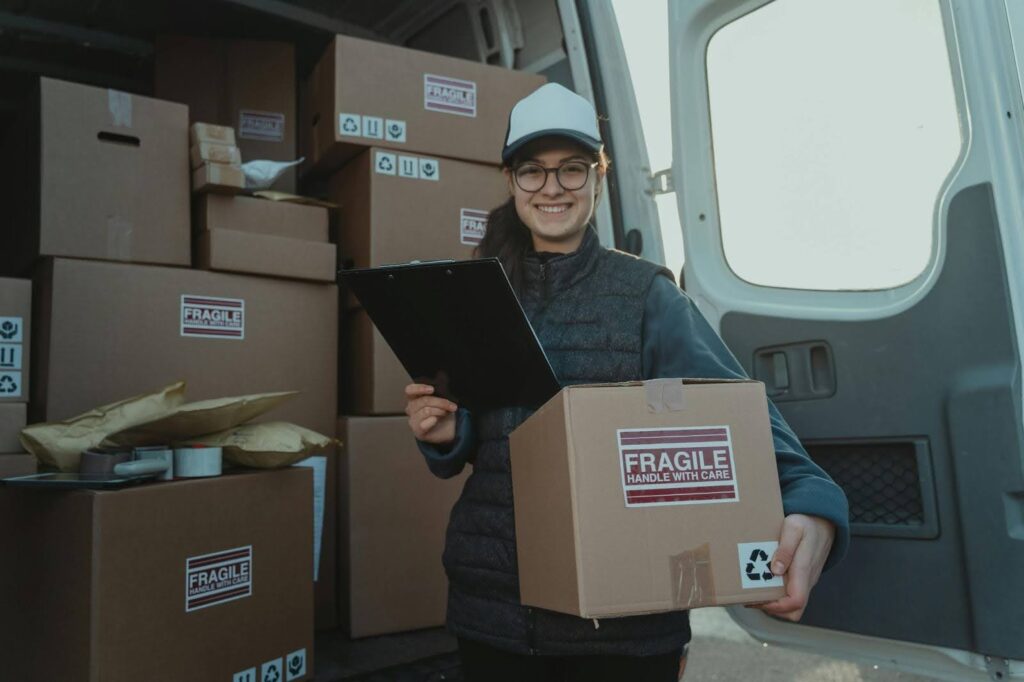
What is a Vendor in the Supply Chain: Types, Key Responsibilities, and Financial Considerations
Running a successful supply chain starts with one question: What is a vendor? Vendors are essential to supply chain success. They are business entities that supply goods or services to other businesses or individual consumers. To describe their role more clearly, a vendor is specifically the party that is paid for goods and services, distinguishing […]
Read More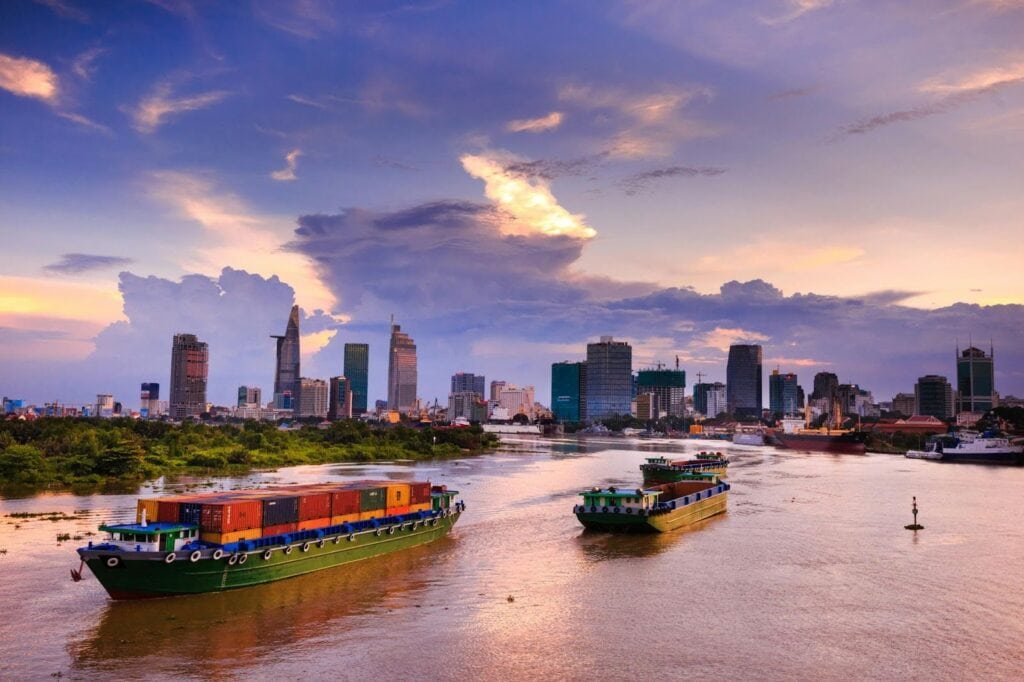
What Is a Consignee in Shipping?
In every international shipping process, someone must take ownership of the goods once they arrive. That person or business is known as the consignee, who must be present to accept the shipment. The consignee’s address must be accurately mentioned on shipping documents to ensure smooth transactions and deliveries. So, what is a consignee? A consignee […]
Read More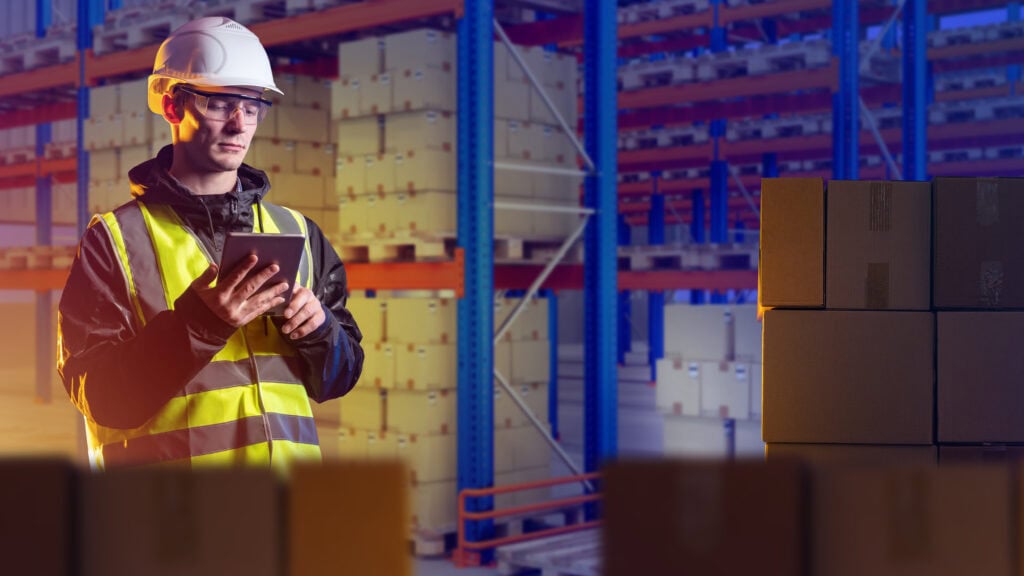
What Is a Bonded Warehouse? Why It Matters More Than Ever in Global Logistics
Whether you’re expanding to new markets, trying to manage costs, or simply looking to strengthen your logistics strategy, bonded warehousing deserves a closer look.
Read More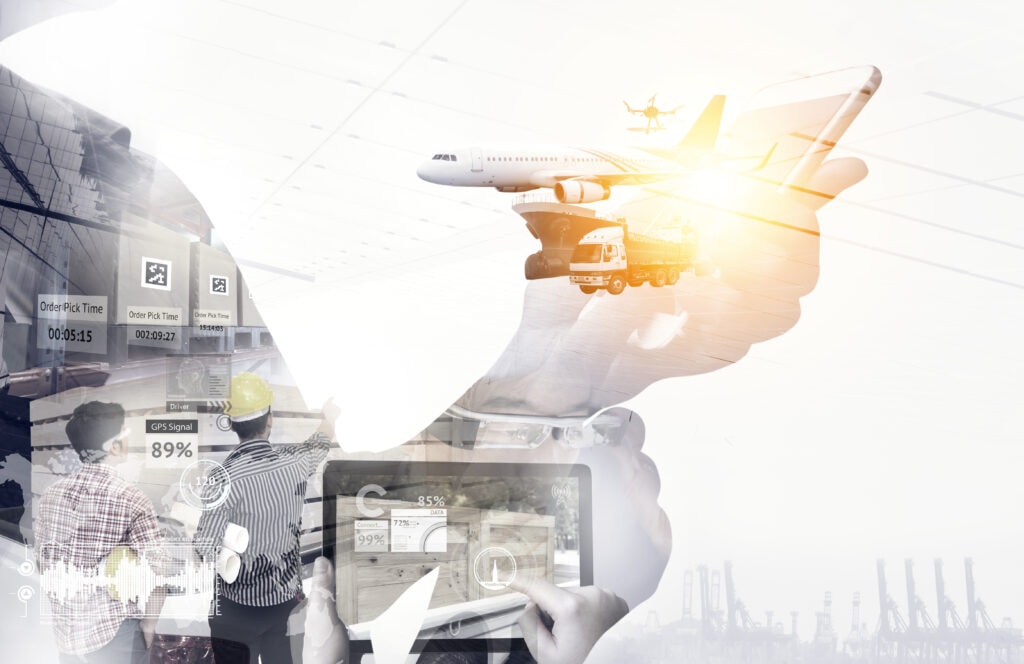
Supply Chain Disruptions: How They Happen, Industries Affected, and How to Manage
Empty shelves. Factory delays. Missed delivery windows. Supply chain disruptions have become more than just industry talk—they’re now everyday realities with direct consequences for businesses, customers, and the global economy. When supply chains break down, the ripple effect reaches every part of operations, from raw materials stuck at borders to finished goods delayed at ports. […]
Read More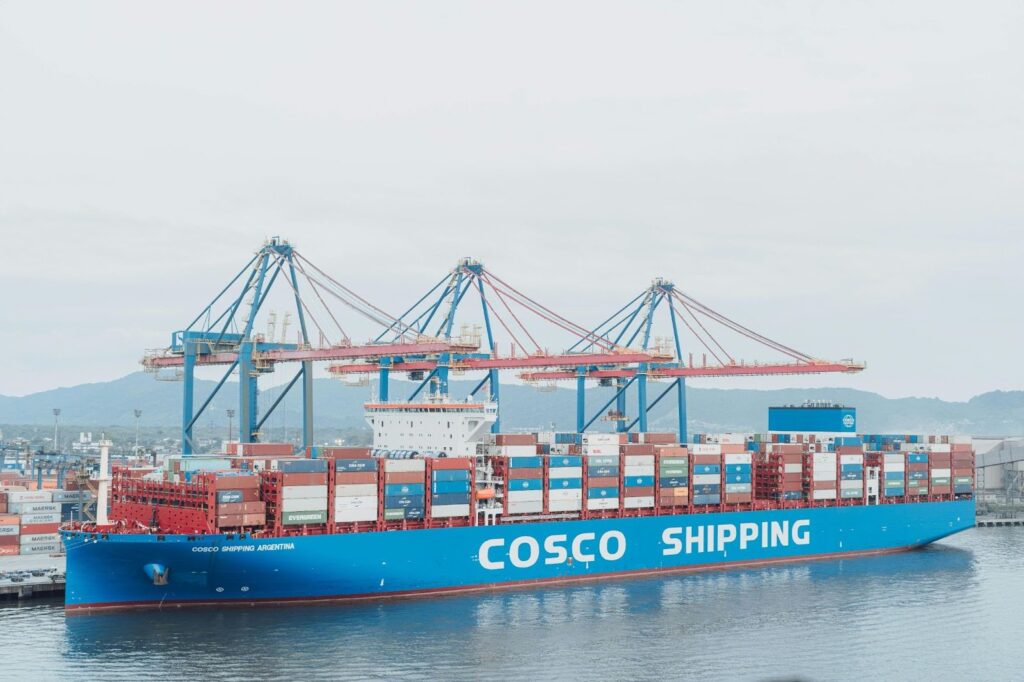
Consignee vs. Consignor: Their Key Shipping Differences
In every freight shipment, two key roles drive the process: consignor and consignee. Without them, no shipment would reach its final destination, and no freight carrier could move cargo efficiently. A consignor is the party sending the goods. Ownership of the goods remains with the consignor until payment is made. The consignee does not own […]
Read More
Navigating Tariff Shifts: How U.S. Foreign-Trade Zones Help Supply Chains Stay Resilient
As global trade faces uncertainty amid shifting tariffs, economic nationalism, and ongoing geopolitical friction, U.S. businesses are increasingly turning to Foreign-Trade Zones (FTZs) as a powerful tool to remain competitive. The U.S. is home to more than 230 approved FTZ projects and nearly 400 subzones, collectively supporting 600+ warehouses across the country. These special zones […]
Read More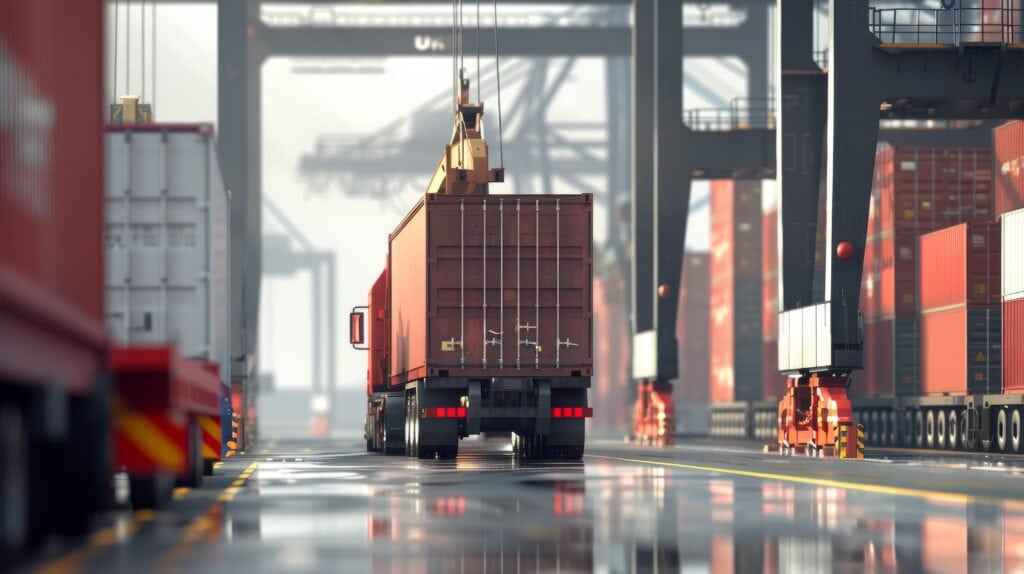
Transloading: Key Benefits and Best Practices for Your Logistics Needs
Discover how transloading can improve your supply chain efficiency. Learn the key benefits, cost savings, and best practices to optimize your logistics operations.
Read More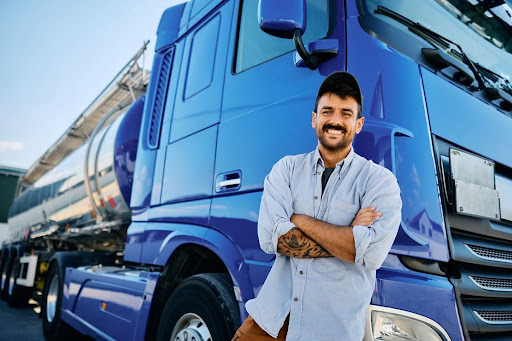
10 Best Trucking Companies to Work For: High Paying Options
Are you a truck driver, whether experienced or a new driver, looking to work for one of the country’s great trucking companies? Are you searching for the best trucking companies to drive for? Below is a list of the top paying trucking companies, as ranked by TruckDriversSalary.com. This article will also highlight companies that provide […]
Read More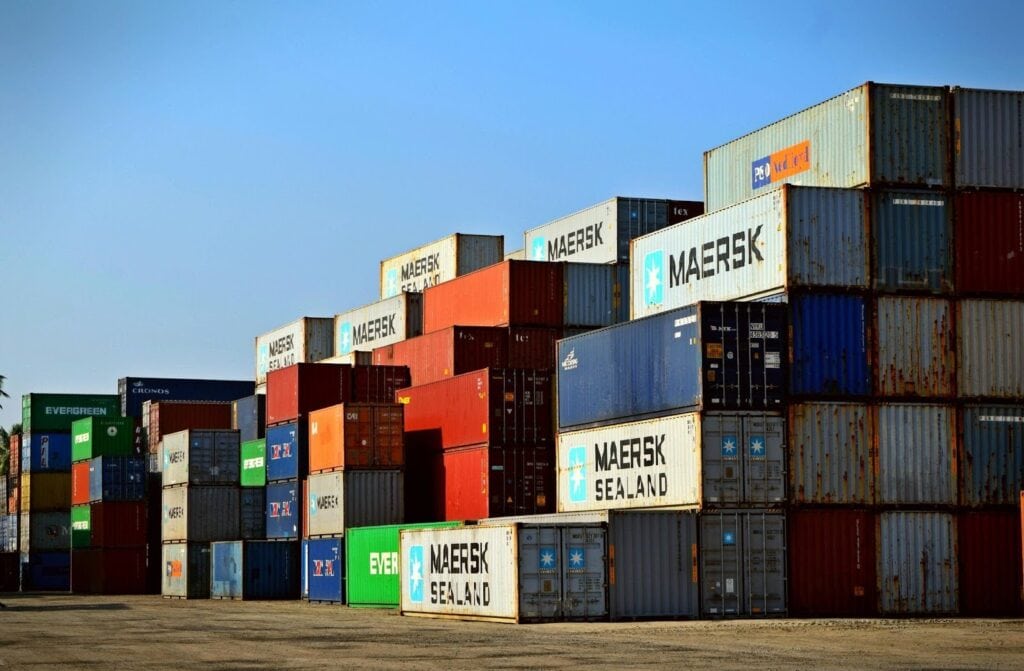
Supply Chain Resilience and Risk Management: Definition, Strategies, and Best Practices
Supply chain management faces unprecedented challenges in today’s supply chains, from natural disasters to fluctuating markets. A robust approach to these hurdles is not just beneficial but necessary. Resilience in supply chains allows businesses to respond swiftly and effectively to unforeseen disruptions, maintaining operational continuity and safeguarding revenue streams. Companies that improve supply chain resilience […]
Read More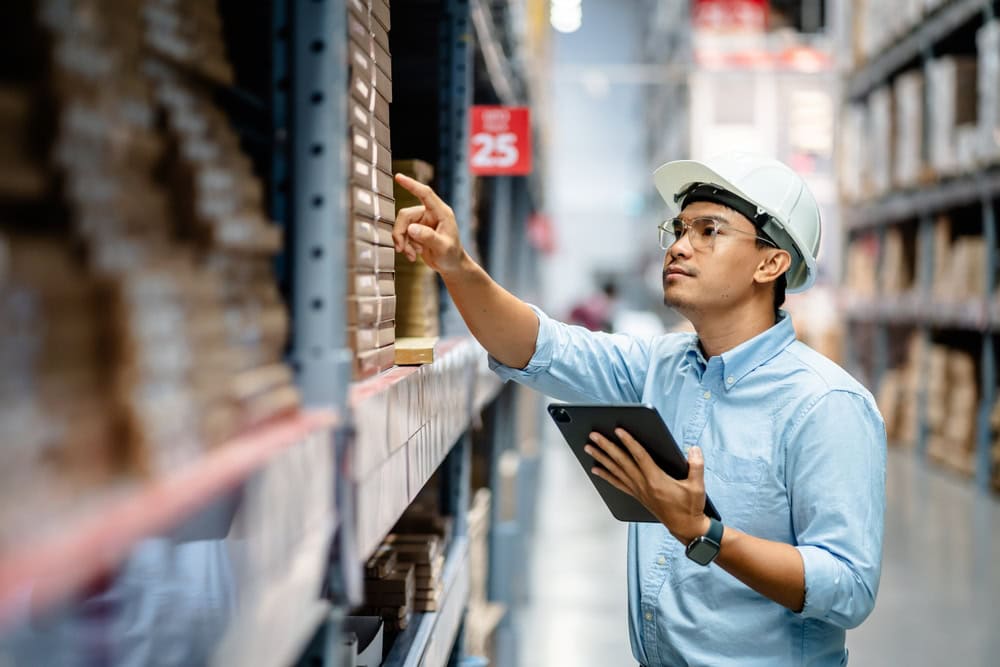
Demand-Driven Supply Chain: Definition, Benefits, and Implementation
A demand-driven supply chain offers significant strategic advantages.
Read More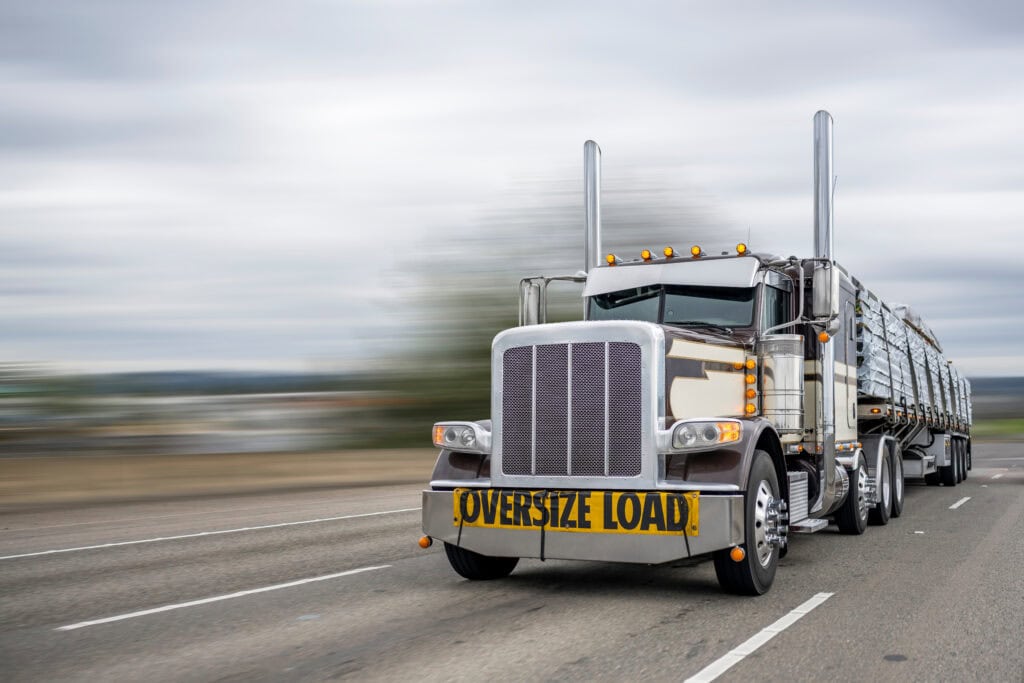
Conestoga Trailers: Definition, Types, and Advantages
Conestoga trailers are a testament to innovation in the trucking industry, transforming the way we transport goods with efficiency and care. With their unique retractable tarping system that shelters goods from the elements while facilitating easy loading and unloading, these trailers have become a linchpin in moving freight efficiently. A survey highlighted that about 65% […]
Read More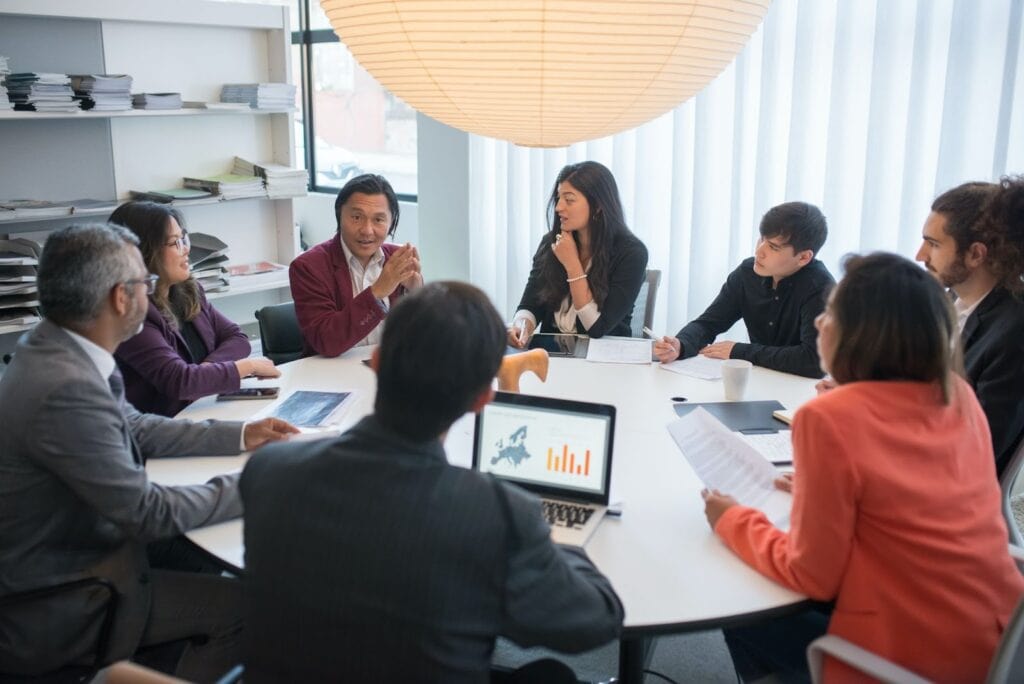
4 Types of Logistics Management
Understanding the different types of material handling equipment is crucial for selecting the most effective solutions to meet specific operational needs. This article explored various categories and types of material handling being used, including storage containers and handling equipment, industrial trucks and machines, bulk material handling equipment, and engineered systems.
Read More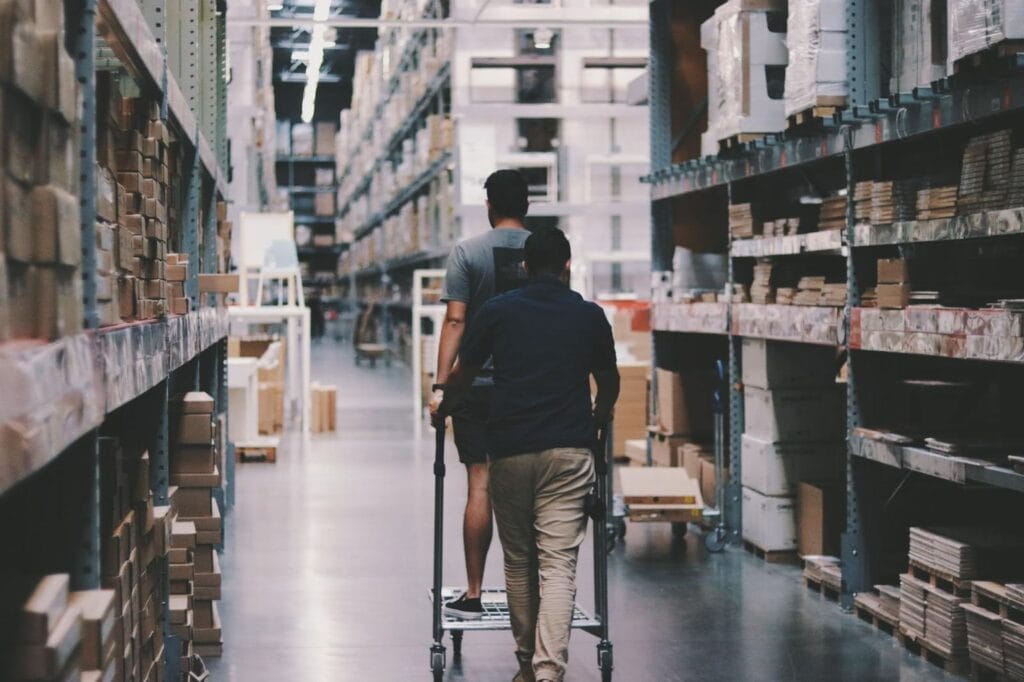
Warehouse Vs. Factory: Purposes and Types of Each
Warehouses and factories, each integral to supply chains and manufacturing, serve distinct yet complementary functions. To optimize logistics, warehouses focus on efficient storage and distribution centers, often situated near key transport routes. Factory features, such as upgraded interiors, modern amenities, and attractive locations, cater to prospective tenants’ lifestyles. Warehouses and factories are vital components […]
Read More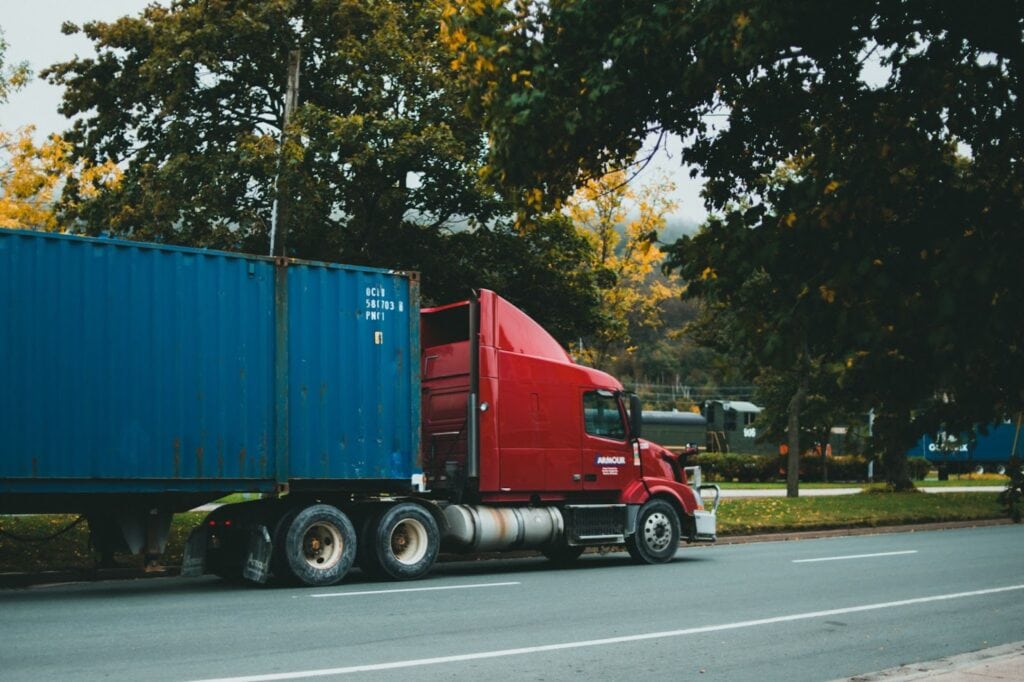
Multimodal Transportation: Definition, Examples, and Advantages
In an era of globalization, where swift and efficient transportation is crucial, the logistics sector has had to innovate and adapt. Among the various evolving transportation services, multimodal transportation stands out as an integrated solution catering to diverse intermodal shipping needs. Let’s delve into this concept and understand its significance in today’s fast-paced world. […]
Read More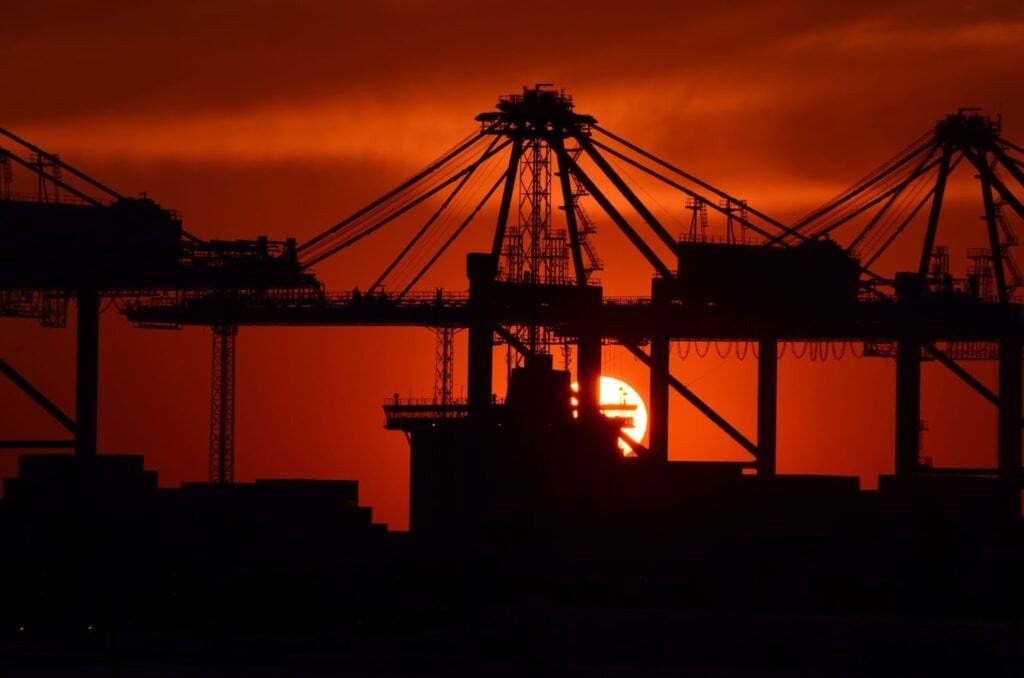
Freight In vs Freight Out: Definitions and Examples
Freight costs are a part of expenses for companies involved in shipping goods and transporting products to customers. Freight services encompass the various costs associated with shipping goods between suppliers and customers. You must understand the difference between freight in vs freight out, regardless of whether you work for a shipping company, a freight company, […]
Read More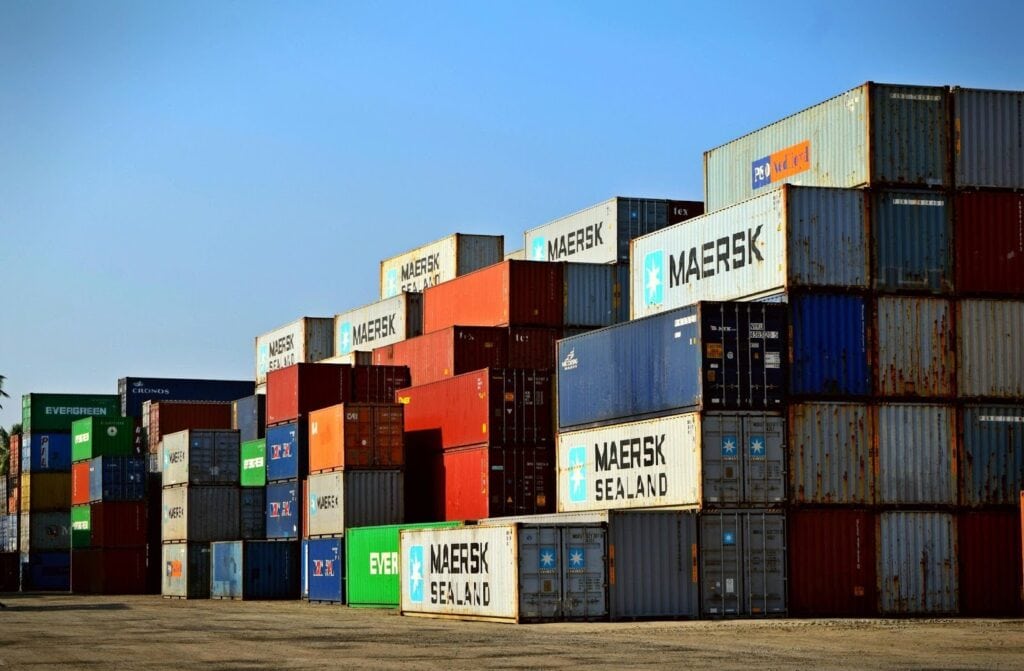
House Bill of Lading vs. Master Bill of Lading – Key Differences Explained
There are distinctions between house bills of lading and master bills of lading. Both help the entire consolidated shipment.
Read More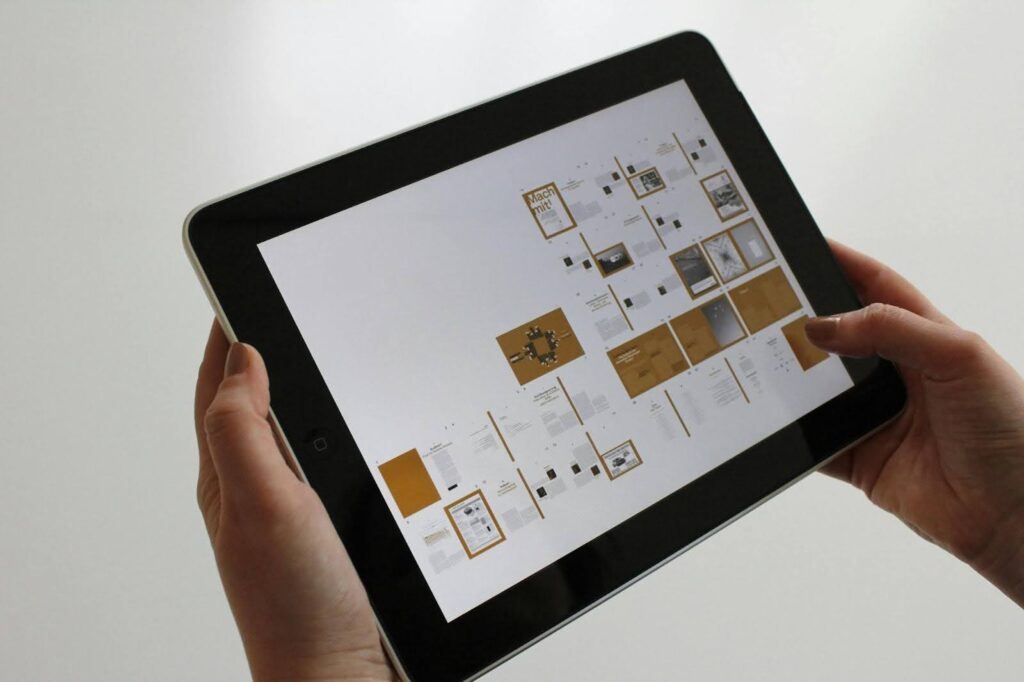
IoT in Logistics: What It Is, Applications, and Benefits
IoT in Logistics: What It Is, Applications, and Benefits As the world becomes more interconnected, the logistics landscape is significantly transforming. Technology has become the backbone of supply chain management, propelling logistics companies into a new era of efficiency and connectivity. Internet of Things (IoT) is a transformative force reshaping the fabric of logistics and […]
Read More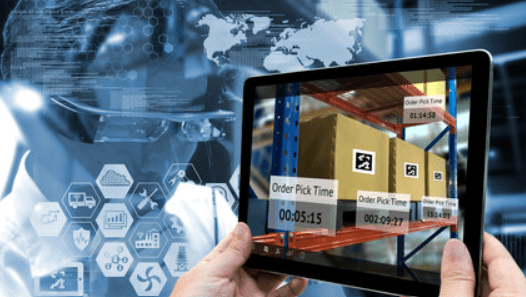
What is Outsourcing? Definition, Advantages, and Examples
Many businesses have successfully adopted outsourcing processes into various aspects of their logistics and supply chain operations. Outsourcing (or out sourcing, as some refer to it) all or part of these functions can improve efficiency and in some cases, reduce costs. Additionally, outsourcing can provide a competitive advantage by accessing specialized expertise and technologies. This […]
Read More